Datendrehscheibe für Energieeffizienz, Produktionsoptimierung und Qualitätssicherung
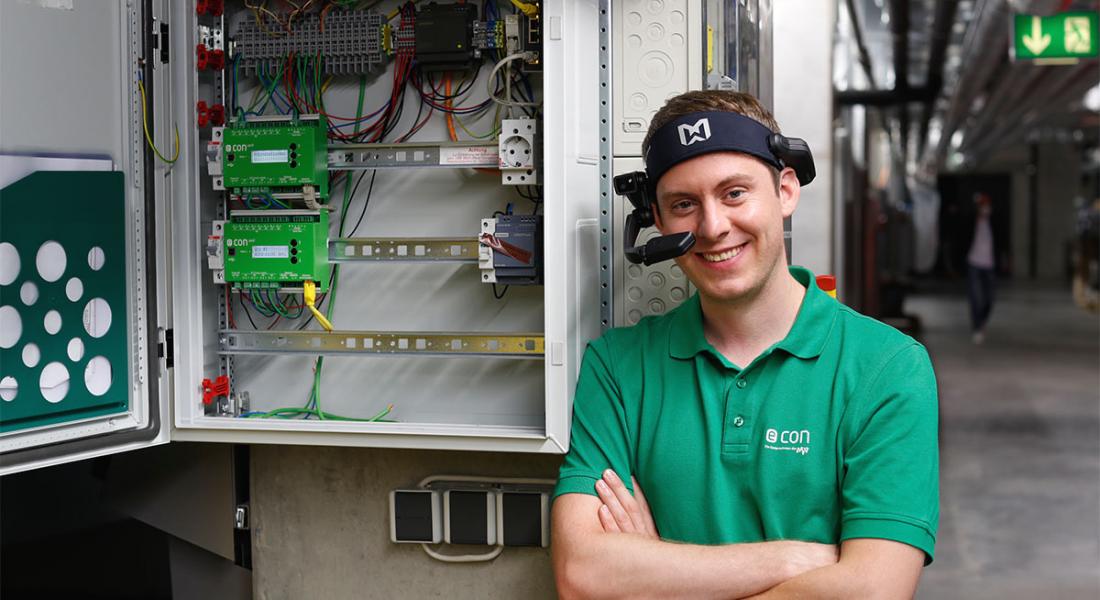
Für das betriebliche Energiemanagement ist nicht der reine Verbrauch entscheidend. Denn der hängt unmittelbar mit der Produktion, der Fläche oder anderen Größen zusammen. Deshalb gilt es, Daten aus Geräten, Maschinen und Systemen in die Energiemanagement-Lösung zu integrieren. Am einfachsten gelingt das mit hardwareunabhängigen Systemen. Zudem bieten Software-Schnittstellen Vorteile gegenüber Hardware-Lösungen.
Für produzierende Unternehmen ist die entscheidende Kennziffer beim Energiemanagement meist der Energieverbrauch pro produziertes Teil, pro Charge oder Tonne. Auch der Verbrauch eines Prozesses oder Bereichs im Verhältnis zum Gesamtenergieverbrauch oder die Energiekosten im Verhältnis zu den Produktionskosten können sinnvolle Kennzahlen sein. Manchmal kommen weitere Abhängigkeiten dazu, z.B. Temperatur, Luftfeuchtigkeit o.ä.. Bei Bürogebäuden oder Lagern ist die relevante Größe häufig der Wärmemengenverbrauch pro Quadratmeter in Abhängigkeit der Außentemperatur.
Geräte und Systeme verschiedener Hersteller
Die meisten der dafür nötigen Daten liegen in den Unternehmen bereits vor, jedoch in unterschiedlichen Systemen und Geräten von verschiedenen Herstellern.
Die simpelste Methode, um sie in das Energiemanagement-System zu übernehmen, ist mittels csv-, txt- oder xsl-Dateien. Damit lassen sich z.B. mit Zeitstempel versehene Stückzahlen gesammelt in regelmäßigen Zeitintervallen übertragen.
Nachteil dieser Variante gegenüber einer direkten Anbindung der entsprechenden Geräte und Systeme: Die Daten liegen nicht fortlaufend vor. Eine Auswertung quasi in Echtzeit ist wie eine Alarmierung beim Erreichen von Schwellwerten nur mit Zeitversatz möglich, der sich aus dem Importintervall ergibt.
Dazu müssen die Maschinen, Geräte und Systeme mit dem Energiemanagement-System verknüpft werden. Die größte Herausforderung dabei liegt in der Vielzahl der vorhandenen Protokolle. Denn in der Regel ist die Infrastruktur in Unternehmen über viele Jahre gewachsen und es finden sich zahlreiche Maschinen, Geräte und Systeme verschiedener Hersteller.
Messgeräte und Sensoren für die Erfassung von Wärme-, Wasser-, Gas- oder Strommengen nutzen üblicherweise Modbus oder M-Bus. Um ihre Messwerte in das Energiemanagement-System zu integrieren, kann ein Datenlogger eingesetzt werden. Er fungiert als Zwischenspeicher und Konnektor. Der Datenlogger econ unit+ V2 von econ solutions verfügt über sämtliche gängige Schnittstellen (S0-Impuls, M-Bus, Modbus, digitale und analoge Signale). Er integriert sich in jede bestehende Infrastruktur, auch in ein BACnet/IP oder Modbus TCP Netzwerk.
Häufig sind diese Messgeräte und Sensoren bereits in eine Gebäudeleittechnik (GLT) oder Betriebs- oder Maschinendatenerfassung (BDE/MDE) eingebunden. Diese basieren entweder auf dem OPC- (OPC UA) oder BACnet-Protokoll. Um die relevanten Daten aus diesen Systemen in das Energiemanagement zu integrieren, bedarf es entsprechender Server und Schnittstellen. Sie einzurichten und Parametrierungen vorzunehmen, erfordert einen relativ hohen Programmieraufwand und Kenntnisse in Programmiersprachen. Deshalb setzen viele Unternehmen hierfür auf Dienstleister.
Software-Schnittstellen vereinfachen Parametrierung
Einen anderen Ansatz verfolgt econ solutions: Mit econ connect bietet der Energiemanagement-Spezialist ein Werkzeug, mit dem Unternehmen die Anbindung von Geräten und Systemen ohne IT-Kenntnisse und mit überschaubarem Aufwand selbst durchführen können. Über eine grafische Oberfläche mit Benutzerführung werden die Schnittstellen der zu übernehmenden Werte und Datenpunkte über eine Tabellenzuordnung eingerichtet. Eine Überwachungsfunktion meldet, wenn Daten nicht oder nicht korrekt im System ankommen.
econ connect deckt sämtliche gängigen Schnittstellen Software-basiert ab (OPC DA/UA, BACnet, Modbus TCP und Modbus RTU). Außerdem unterstützt econ connect den Import von per E-Mail verschickten Dateianhängen (MSCONS, csv, txt) sowie die Direkteinbindung des Energie- und Leistungsmessgeräts econ sens über die IP-Adresse. Darüber hinaus können auch csv, API, MSCONS, Wago und damit KNX, Profibus, LON und weitere Schnittstellen an das econ-System angebunden werden. Bei Bedarf integriert econ solutions auch proprietäre Protokolle nach Prüfung mit dem Hersteller. Alle Schnittstellen lassen sich beliebig kombinieren.
Daten werden zu Bildern und zu Erkenntnissen
Das Landtechnikunternehmen Fendt hat seine Gebäudeleittechnik und die Anlagentechnik „Fendt View“ via OPC und BACnet mit Hilfe der econ connect Software-Schnittstellen an das Energiemanagement-System angebunden. Aus diesen laufen u.a. die Temperatur von Anlagen und Außenluft, Feuchtigkeit, Volumenströme, Beleuchtungszeiten sowie Steuersignale vom Band in die Energiemanagement-Software econ4. Sie erstellt daraus und aus den Werten weiterer Messgeräte die entscheidende Kennziffer für Fendt, den Energieverbrauch pro gefertigten Traktor, sowie zahlreiche Auswertungen. Auf dieser Basis konnte Fendt durch eine Reihe gezielter Effizienz-Maßnahmen den Verbrauch pro Traktor deutlich reduzieren.
Die Wäscherei Merz in Wurmberg bei Pforzheim kombiniert die Energiedaten mit Stückzahlen und Gewicht der Wäschestücke sowie Durchlaufzeiten und Geschwindigkeiten aus Lichtschranken, CPU, Leistungsklemmen und Stromzählern von Wago. Weitere Leistungskennzahlen fließen aus der ERP-Software Tikos von Socom ein, die Merz bereits im Einsatz hatte. Mit den daraus erstellten Analysen kann Merz detailliert den Energie-, Gas- und Wasserverbrauch nachvollziehen, Strom-Spitzenlasten vermeiden und Schäden an Maschinen frühzeitig beheben. Außerdem liegt eine fundierte Kalkulationsbasis für einzelne Textilien oder Aufträge vor.
Bei der Brauerei Dinkelacker-Schwabenbräu dient das Energiemanagement-System darüber hinaus als Basis für Investitionsentscheidungen: Aus den Kennlinien der Kompressoren hat der Leiter Instandhaltung und Energie mathematische Modelle entwickelt, mit denen er für verschiedene neue Kompressorenmodelle unterschiedliche Szenarien durchspielen und monetär bewerten kann.
Ensinger Mineral-Heilquellen hat mit der Lösung nicht nur den Energieeinsatz pro 1.000 abgefüllter Flaschen analysiert und reduziert, sondern nutzt diese Kennziffer auch, um Maschinendefekte frühzeitig zu erkennen.Vorher waren diese lange unentdeckt geblieben und währenddessen für einen erhöhten Verbrauch gesorgt. Zudem fließen bei Ensinger Daten von Messgebern unterschiedlicher Maschinen in das Energiemanagement-System, etwa der pH-Wert, die Leitfähigkeit und Temperatur. Die Software econ4 generiert daraus Schaubilder, welche die Produktionsleiter täglich auf ihre Rechner erhalten. „Mit Energiemanagement hat das zwar gar nichts mehr zu tun, aber die Messgeräte lassen sich so einfach einbinden und die Produktionsleiter sehen sofort, wenn trendmäßig etwas aus dem Ruder läuft“, erklärt Siegfried Winkler, technischer Leiter und Energiebeauftragter bei Ensinger.