Locating compressed air leaks: good for costs and the climate
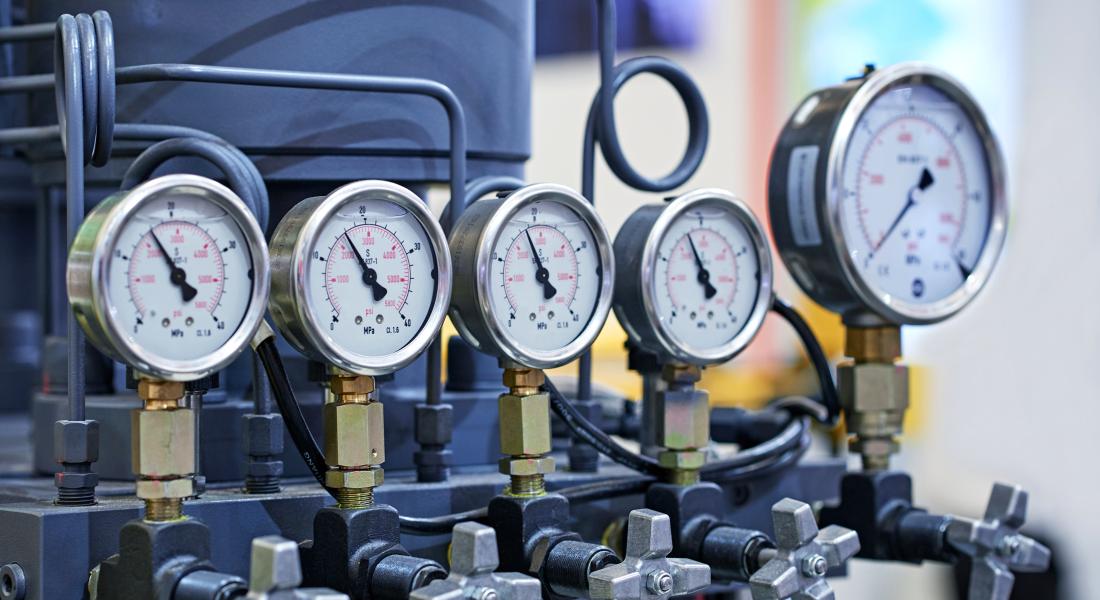
Compressed air is not only one of the most common forms of energy in industry, it is also one of the most expensive. For this very reason, companies should examine every opportunity to make savings. Locating and eliminating leaks in the compressed air network offers great potential. This not only reduces energy costs for compressed air generation, but also CO2 emissions.
Compressed air is used to clean workpieces, control valves, transport materials, supply pneumatic drives and optimize processes. In a nutshell: this extremely versatile medium plays an important role in many areas of industry.
However, a fundamental problem with compressed air generation is the losses caused by leaks, which often go unnoticed for a long time. It is important to know that leaks in compressed air systems are unavoidable. Due to the size of the network, medium-sized companies always have a five to 15 percent loss of efficiency due to leaks. However, for anything above this, the leaks should be localized, eliminated and documented as a matter of urgency.
Permanent compressed air losses
Leaks in a pipe network act like nozzles from which compressed air flows out at high speed - 24 hours a day. To compensate for the resulting pressure losses, unnecessary energy has to be used for the compressors. Although they can be switched off when no compressed air is needed, the pressure vessels lose the compressed air produced up to atmospheric pressure. When the compressors are restarted, the tanks have to be refilled to operating pressure, which again costs energy.
According to a study on energy and cost savings potential in fluid technology by the Federal Environment Agency, an estimated 80 percent of compressed air systems have leaks in the central compressed air network, in which up to 30 percent of the compressed air is lost. In the long term, leaking air can become a cost driver for companies, as generating compressed air is energy-intensive and therefore expensive.
Leaks cost money and harm the climate
After electricity, compressed air is the second most common energy source in manufacturing companies. Around 60,000 compressed air systems are in operation in Germany, which together consume around 16 terawatt hours per year. That is seven percent of the total electricity consumption of German industry.
If there are leaks in the compressed air network, the compressor has to run for longer, which requires more electricity. A single leak of 50 liters of compressed air per minute can cost as much as 900 euros a year. As multiple leaks often occur, the costs can quickly add up to several thousand euros per year. The identification and elimination of compressed air leaks is therefore also considered to be the single measure with the greatest energy-saving potential in the supply of compressed air.
However, leaking pipes not only drive up costs, but also have a negative impact on the climate. This is because the additional power consumption by the compressors also releases unnecessarily large amounts of CO2.
Various causes for leaks
The reasons for losses in the compressed air network vary greatly. Possible causes include
- Leaking couplings and hose clamps
- Leaking screw and flange connections
- Leaking weld seams and soldered joints
- Porous or defective hoses
- Porous or defective seals on tools and machines
- Defective condensate separators
- Leaking or improperly installed dryers, filters or maintenance units
- Corroded pipes
Many leaks are not detected in the often widely branched compressed air networks. They are often so small that they are barely or not at all visible to the naked eye. In addition, compressed air is odorless and production noise can mask the noise of the escaping air. Even when production is at a standstill, the leaks are usually not audible: Only around 20 to 30 percent of leaks are noticeable due to hissing or other noises. The human ear does not perceive the remaining 70 percent.
Making leaks audible and visible
A reliable and widespread method for identifying and eliminating compressed air leaks today is the use of ultrasonic testing devices. Modern, portable ultrasonic detectors are used to quickly and accurately identify even less obvious leaks in the compressed air network, even during operation. The leak detectors measure the ultrasound generated by compressed air leaks and reproduce the ultrasound source visually and acoustically. They detect sound waves in a frequency range that cannot be perceived by the human ear. With the advanced sensor technology, the devices can detect even the smallest leaks of 0.1 liters per minute. This corresponds to a loss of around one euro per year.
In a very noisy production environment, headphones help to precisely locate the leaks. With the help of a parabolic mirror, the smallest leaks can be detected even at great distances of up to 20 meters. For pipes that are difficult to access, a flexible probe (gooseneck) increases the user's range.
Professional data management
After successful detection, all the necessary information about the leak can be stored in new, state-of-the-art leak detectors and a picture of the leak can be taken with the integrated camera. All the information required to eliminate the leak is thus documented directly on site. Once all leaks have been identified, all data and photos are saved and can then be imported directly into the management tool of the econ4 software from MVV's solution house partner econ solutions. A specific measure is created for each leak, which can be assigned to any person for elimination. Those responsible can then immediately see exactly where the leak is, how much compressed air is escaping, how high the estimated savings potential is and what needs to be done to rectify the leak.
Major savings in costs and CO2 emissions
Regularly locating and eliminating leaks, which are often only millimeters in size, pays off for companies. Between 9 and 16 percent of energy can be saved with this measure. The climate also benefits: with an annual electricity requirement of 16 terawatt hours for the supply of compressed air, this corresponds to a savings potential of 1.44 to 2.56 terawatt hours or a saving of 0.54 to 0.98 million tons of CO2 per year.
Benefit from the expertise of the MVV Solution House
Compressed air generation is energy and cost-intensive. Leaks in compressed air systems not only result in increased energy consumption, they also unnecessarily release large quantities of CO2. With the help of ultrasonic leak detection, leaks can be detected and eliminated immediately.
econ solutions and BFE Institute for Energy and Environment are specialists in energy management and experienced in locating compressed air leaks. Using state-of-the-art ultrasonic testing equipment, the experts can precisely locate leaks in your compressed air system, enabling you to increase energy efficiency. Your benefit: you can immediately cut costs, make production more efficient and reduce your CO2 footprint in the long term.