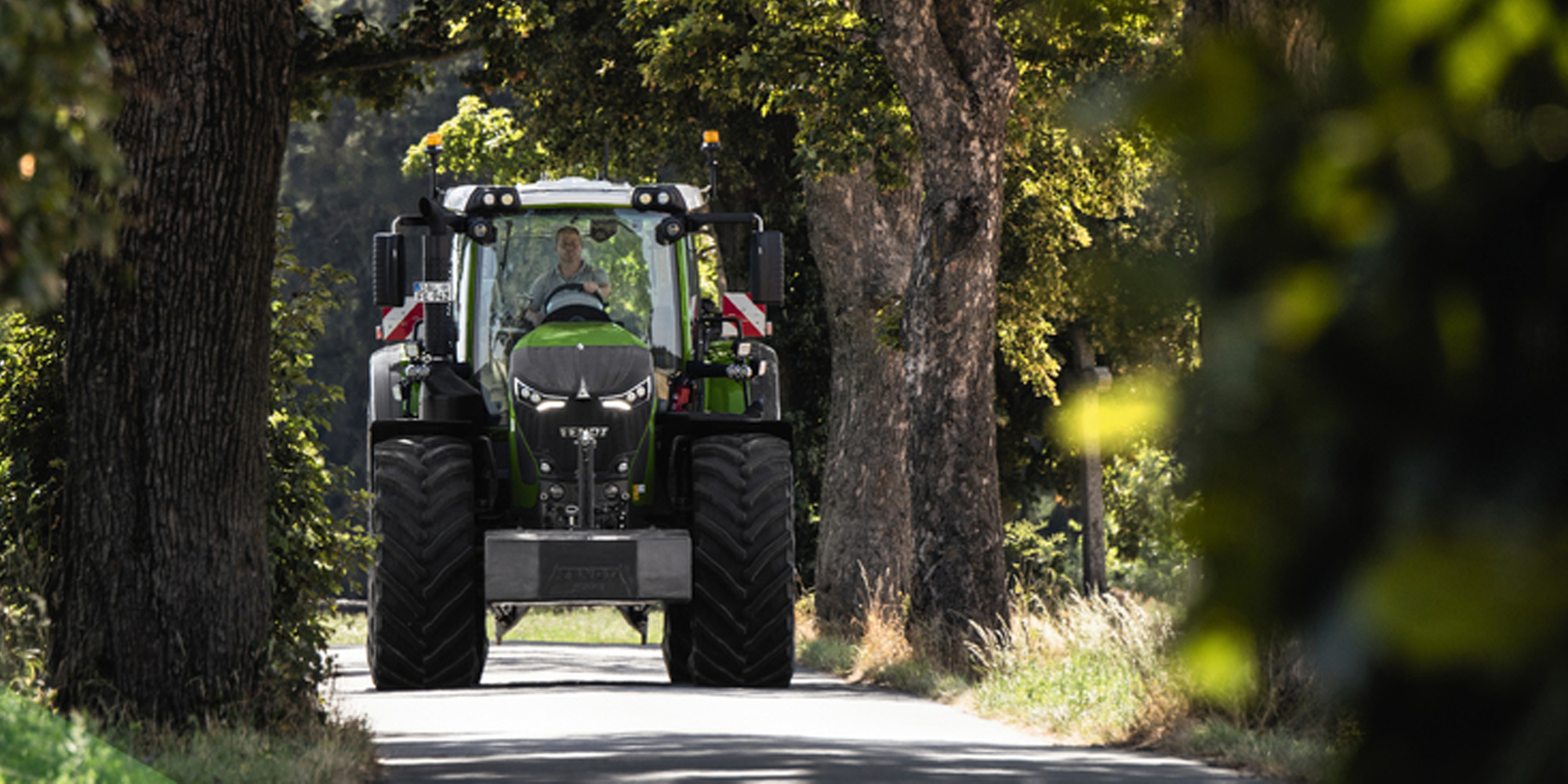
AGCO Fendt
Close to nature, efficient in production
The agricultural machinery company Fendt is close to nature with its products. That is why the manufacturer is also committed to protecting and preserving it. Sustainability in its own production is a central component of this. It is constantly being improved with comprehensive energy management, supported by the solution from econ solutions.
When it comes to energy generation and energy consumption in production, Fendt relies on four building blocks: measurement, avoidance, reduction and substitution. For a long time, measurements were carried out manually and the data was recorded and analyzed in Excel. "We had a lot of data, but little transparency," explains Markus Lihs, environmental and energy specialist at AGCO, Fendt's parent company. For more transparency, a professional tool was needed that would enable the automated recording and evaluation of energy-relevant data.
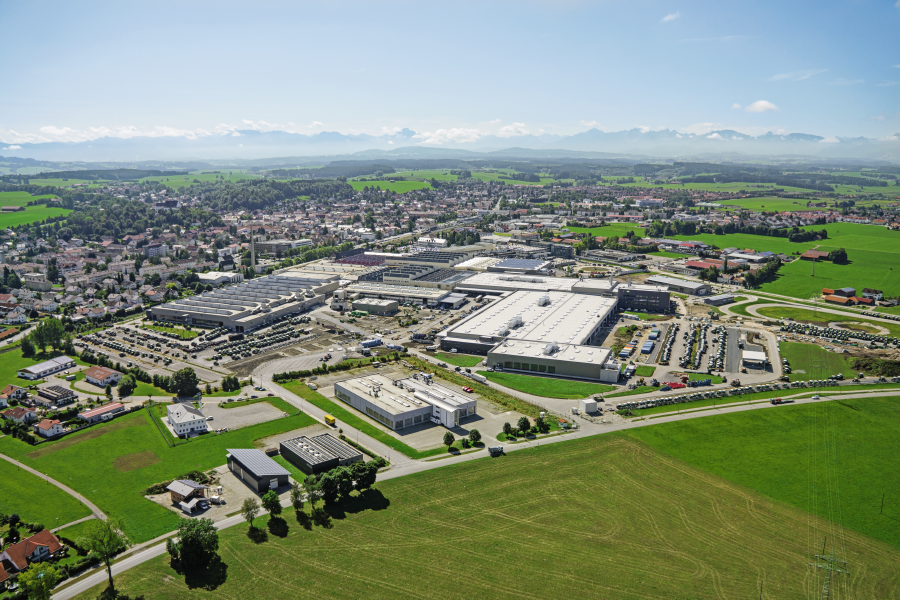
In einem Pilotprojekt analysierte und bewertete das Energieteam mit Unterstützung von zwei Bachelor- und einem Master-Studenten und dessen Masterarbeit „Implementierung einer Energiemanagement-Software“ mehrere Energiemanagement-Systeme von namhaften Herstellern. Diese kamen am Hauptstandort Marktoberdorf zum Einsatz, an dem sich die Entwicklung und Produktion der Fendt Traktoren befindet, sowie in Asbach-Bäumenheim, wo die Kabinen und Hauben für einen Großteil des Konzerns gefertigt werden. Das Ergebnis der Testphase: Die Lösung von econ solutions bietet das beste Preis-Leistungs-Verhältnis und die besten Erfolgsaussichten für ein nachhaltig wirkungsvolles Energiemanagement.
In Sachen Messtechnik hat Fendt zuerst die steuerrelevanten Zähler in das econ System integriert, inzwischen erfasst das Unternehmen mit rund 540 Messstellen den gesamten Energieverbrauch an beiden Standorten inklusive Außenstellen. Neben dem Umfang wurde auch die Messtiefe sukzessive erweitert; sie reicht jetzt in einigen Bereichen bis hinunter zu Maschinen mit einem Verbrauch von 1kWh. Zähler und Sensoren, die bereits vorhanden waren, kommen weiterhin zum Einsatz, da das econ System herstellerneutral die Anbindung verschiedenster Messgeräte erlaubt. Für neu geschaffene Messstellen nutzt Fendt das Energie- und Leistungsmessgerät econ sens3. Es ist klein und dank mehrerer Schnittstellen auch in bestehende Systeme schnell und unterbrechungsfrei eingebaut.
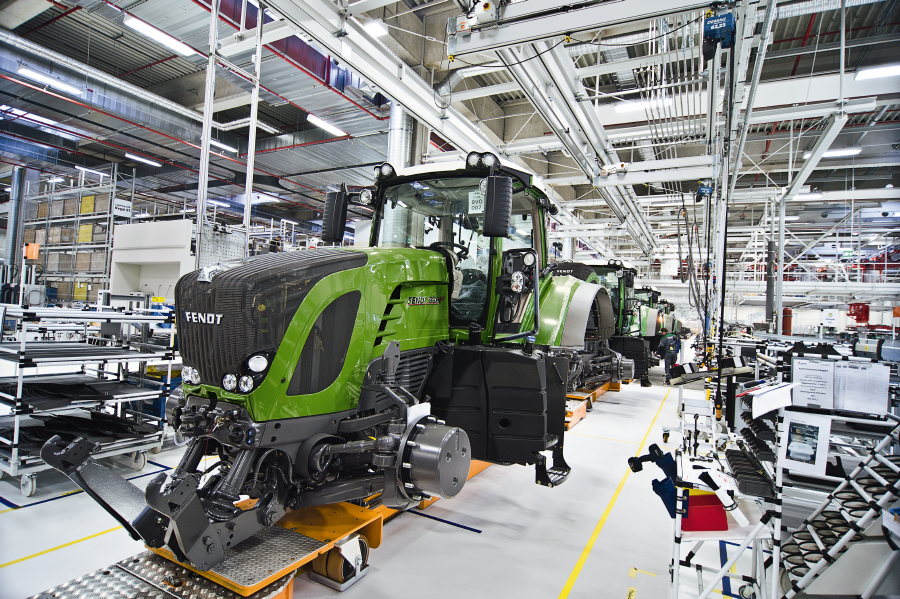
Anbindung der Anlagen- und Gebäudeleittechnik
Die Gebäudeleittechnik (GLT) und die Anlagentechnik „Fendt View“ wurden über die econ connect Softwareschnittstellen via OPC und BACnet angebunden. Hierfür mussten seitens der GLT zum Teil neue Schnittstellen geschaffen werden, die Koordination mit den entsprechenden Anbietern hatte econ übernommen.
Aus der Anlagen- und Gebäudeleittechnik laufen zahlreiche weitere Daten in die Energiemanagement-Software econ4, darunter die Temperatur von Anlagen und Außenluft, Feuchtigkeit, Volumenströme, Beleuchtungszeiten sowie Steuersignale vom Band. Aus diesen und den Werten der Messgeräte erstellt die Software in einem umfangreichen Berichtswesen zahlreiche Auswertungen sowie Kennzahlen – so auch die entscheidende Kennziffer für Fendt, den Energieverbrauch pro gefertigten Traktor.
Diese Kennziffer konnte Fendt durch eine Reihe an Effizienz-Maßnahmen bereits deutlich verbessern: So ist durch die Auswertungen zum Beispiel aufgefallen, dass die regenerative Nachverbrennung für die Abgasnachbehandlung auch in den produktionsfreien Nachtstunden geheizt wurde. Die Heizzeiten konnte Fendt mühelos anpassen und damit Energie einsparen.
Zudem übermittelt Fendt für jede Woche die Produktionszeit, Neben-, Rüst- und Stillstands-Zeit sowie die Zeit für Einfahrteile an econ. econ4 errechnet den Energieverbrauch in den jeweiligen Phasen. Dadurch zeigte sich z.B., dass eine Maschine für die Zahnradfertigung in der Stillstandszeit, also im Stand-by-Betrieb, noch 20kWh verbraucht. Sie lässt sich jedoch auch so abschalten, dass sie mit 3kWh auskommt, ohne dass dadurch irgendwelche Nachteile entstehen. Bei zwanzig Maschinen ergibt sich daraus ein nicht unwesentlicher Effizienzgewinn. „Damit wir die Einsparungen auch in Euro beziffern zu können, haben wir für Strom, Wärme, usw. Preise hinterlegt“, berichtet Markus Lihs.
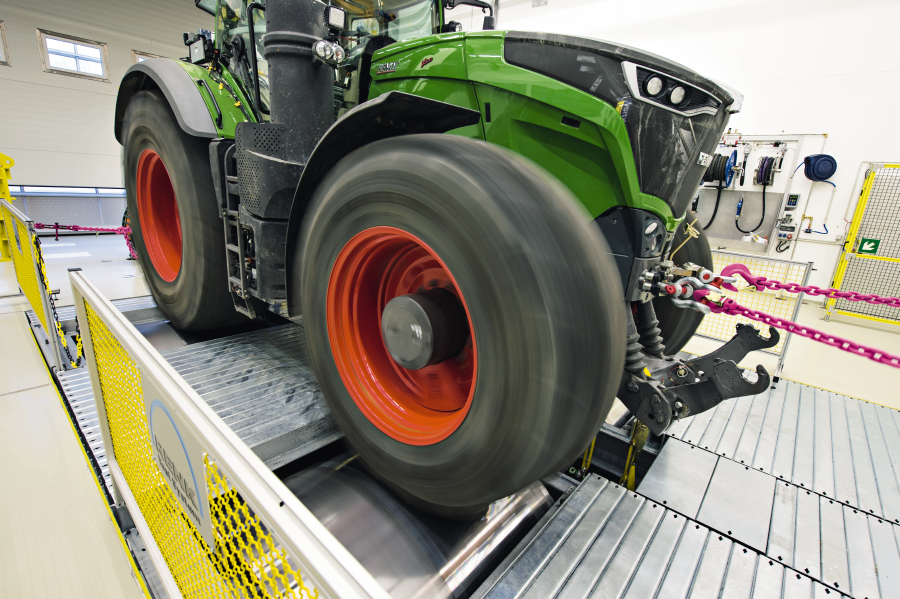
Basis für Managemententscheidungen
Zudem vergleicht das Energieteam die Verbräuche von Maschinen desselben Typs neuerer und älterer Generation, um ihre Amortisationszeit zu ermitteln. Aus den Daten ergibt sich außerdem die Total Cost of Ownership (TCO) jeder Maschine – eine hervorragende Basis für Investitionsentscheidungen.
Um Stromspitzen oder ungewöhnlich hohe Verbräuche im laufenden Betrieb sofort zu erkennen und wenn möglich zu beheben oder mindestens zu reduzieren, hat das Energieteam in econ4 unterschiedliche Grenzwerte hinterlegt. Wird ein Wert erreicht, erhält der entsprechende Anlagenbetreuer per Mail einen Hinweis. „Mit econ haben wir darüber hinaus die Basis für ein wirklich intelligentes Spitzenlastmanagement – das wollen wir demnächst umzusetzen“, so Markus Lihs.
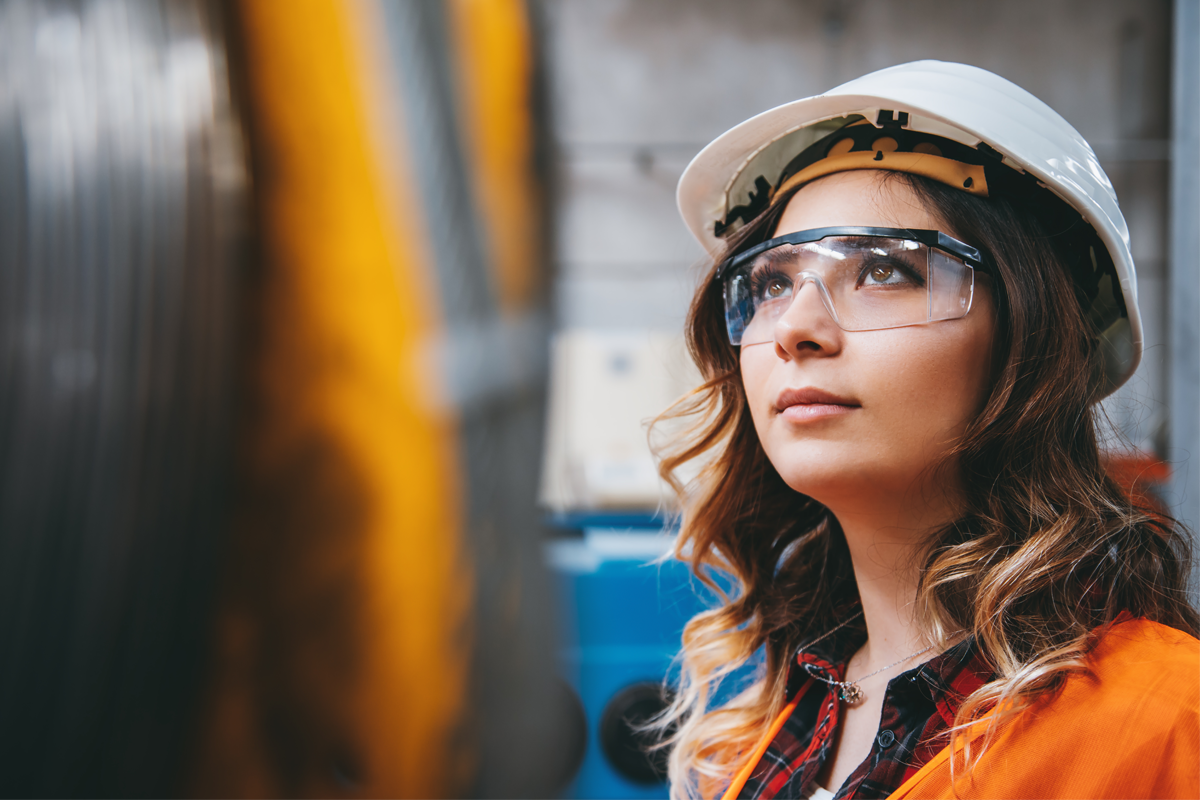
Erfolgsfaktor Mensch
Die Großverbraucher bei Fendt stehen in der Zahnradfertigung, im Getriebewerk und im Traktorenwerk, hier ist es vor allem die Lackierung. Die Betreuer der jeweiligen Maschinen und Anlagen waren neben dem Energieteam bislang die einzigen Nutzer des econ Systems. „Ihr Verhalten ist ganz entscheidend für den Energieverbrauch der Maschinen und Anlagen. Deshalb werden auch die anderen Maschinenbetreuer nach und nach für das econ System geschult. Wenn mehr User damit arbeiten, können wir mit econ noch viel mehr machen“, so Markus Lihs.
Weil die Menschen beim Energiemanagement eine zentrale Rolle spielen, hat auch die unternehmensweite Kommunikation zu den Energiethemen einen enormen Stellenwert. Monatliche Energiereports informieren die Geschäftsführung und die leitenden Positionen bis hinunter zu den Meistern über die entscheidenden Kennzahlen, Verbräuche und Maßnahmen. „Solche Berichte haben wir von Anfang erstellt, mit econ geht das jetzt aber erheblich schneller und einfacher. Es wäre wirklich schade, mit dem System nur Messtechnik zu betreiben!“, ergänzt Lihs. Um die ganze Belegschaft für den Energieverbrauch zu sensibilisieren und an den Erfolgen teilhaben zu lassen, finden sich die Energiethemen auch in der Mitarbeiter-Zeitung und auf Bildschirmschonern.
Über das Vorschlagswesen sind alle Mitarbeiter aufgerufen, Energiespar-Ideen einzubringen. Gibt der Anlagenbetreuer grünes Licht für die Machbarkeit, wird der Vorschlag umgesetzt. Mit Hilfe des econ Systems lässt sich der damit erzielte Effekt sofort ermitteln. Ist dieser positiv und trägt dazu bei, die Energieeffizienz zu erhöhen, kann sich der Ideengeber über eine Bonuszahlung freuen.
Energy consumption decoupled from production volume
With various measures, Fendt was able to save 900,000 kWh of energy at both its Marktoberdorf and Bäumenheim sites in 2019 alone. The company also succeeded in decoupling energy consumption from the increase in production: in 2019, production in Marktoberdorf required over 200 kWh less per tractor than in the previous year. "With econ, we can prove this in detail. The system is like a navigation device on our sustainability journey: it shows us how far we have already come and the most sensible way to move forward," explains Markus Lihs.